8-92-92-36-46-56
с 7-00 до 18-00 мск.вр.
8-922-758-00-88(Viber; Whatsapp; Telegram)
Газобетонное оборудование для производства

газоБетонные комплексы серии «Атлант»
Линия высокой производительности, с электронным дозированием и управлением подачи песка, цемента, воды. С автоматической высокоточной резкой газоблоков.
до 100 м3
в сутки
от 400 м2
помещения
6
рабочих в смену
Высокий уровень выхода готовой продукции

газоБетонные комплексы серии «Антей»
Линии средней производительности, оснащённые бункерами-дозаторами для взвешивания песка и цемента, подающихся ручным или автоматическим способом, с возможностью механизированной резки газобетонного массива на блоки необходимого размера.
до 60 м3
в сутки
от 250 м2
помещения
3-4
рабочих в смену
Быстрый старт бизнеса – быстрое развитие
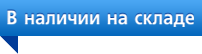
газоБетонные комплексы серии «Феликс»
Линия малой производительности, с ручной или автоматической подачей песка, ручной загрузкой цемента и ручным пилением газобетонного массива.
до 20 м3
в сутки
от 80 м2
помещения
2
рабочих в смену
Начни своё дело прямо сейчас
Работы по оптимизации оборудования на стадии конструирования
В условиях полигонных испытаний были определены два наиболее времязатратных этапа изготовления газобетонных блоков:
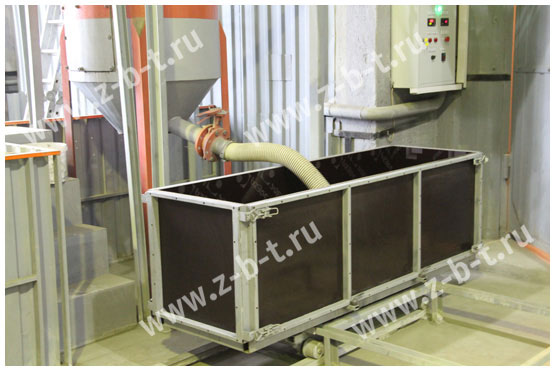
Первый этап — подготовка и заливка форм
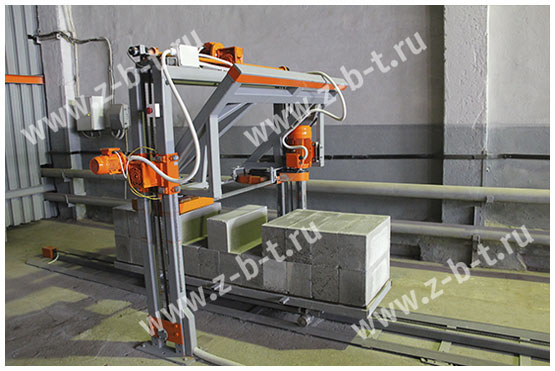
Второй этап — резка газобетонного массива на блоки
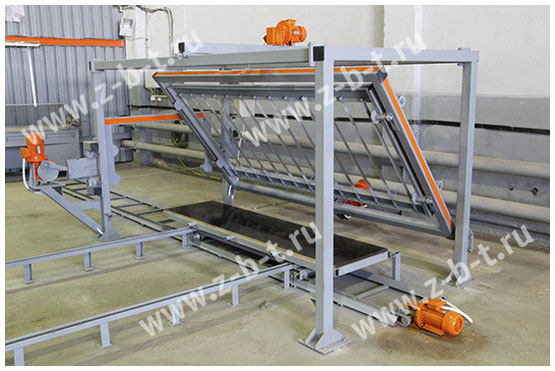
Второй этап — резка газобетонного массива на блоки
Таким образом, одной из основных задач разработки газобетонного оборудования для наших инженеров стала оптимизация процесса производства газобетона за счёт сокращения времени, затрачиваемого на данные этапы.
Подготовка и заливка форм
Для решения проблемы этого этапа производства газобетонных блоков требовалось устранить конструктивные изъяны принятых размеров форм, а также заменить материал их бортов. Ранее формы для производства газоблока, ширина которых превышала 600 мм, приходилось пропиливать вдоль на расстоянии от 1,2 до 2 м. По причине технической сложности точного выполнения таких манипуляций при помощи струнного резака, значительная часть получаемых блоков не соответствовала нужным размерам.
Что касается материала бортов форм – выполненные из листового металла, они не позволяли достичь герметичности прилегания. Плотно прижать борта форм друг к другу, исключив течь, без применения уплотнителя не предоставлялось возможным. А склонность листового металла к деформации лишь усугубляла эту проблему.
Замена металла фанерой с ламинированными внутренним и наружным слоями позволила добиться герметичности между бортами, ускорить процесс подготовки форм, исключить прилипание газобетонного массива к их бортам и упростить разбортовку.
Резка газобетонного массива на блоки
Резка массива на газобетонном оборудовании средней и высокой производительности ранее осуществлялась по струнному принципу.
Недостаток этой технологии заключался в невозможности сохранения струнами постоянного и равномерного натяжения и происходящих вследствие этого их растяжением и обрывами. К тому же, малопроизводительный кривошипно-шатунный механизм привода струнного резака не подходил для обслуживания большого количества форм.
Поворотная рама, лежащая в основе механизма комплекса «ПАРУС», позволила избавиться от двух приводов и двух ленточных полотен с маховиками. Комплекс последовательно делает запрограммированные вертикальные и горизонтальные резы. Весь процесс автоматизирован. Комплекс работает по принципу "одной кнопки".
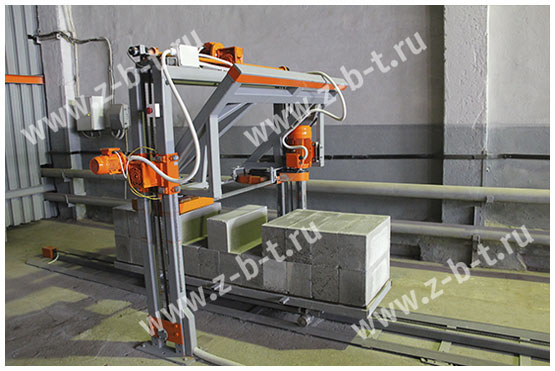
Установка «ПИРАНЬЯ» работает в два этапа. Сначала опускающаяся пильная рама делит массив на необходимое количество блоков заданной геометрии по вертикали, затем массив наезжает на стационарную пильную раму, тем самым производятся три горизонтальных реза.
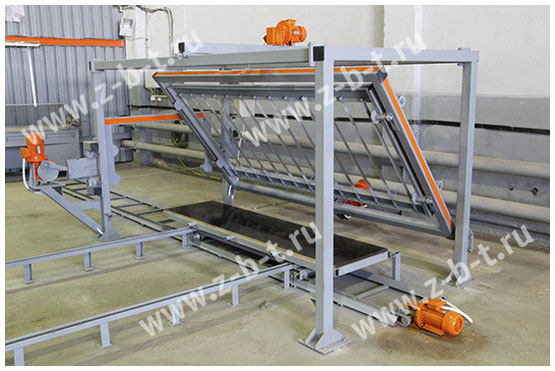